В доменном цехе №2 НЛМК внедрили новый цифровой сервис, который в режиме реального времени отслеживает движение сырья и его состав
Это позволяет не только повысить эффективность производства, но и сделать процесс более устойчивым и предсказуемым.
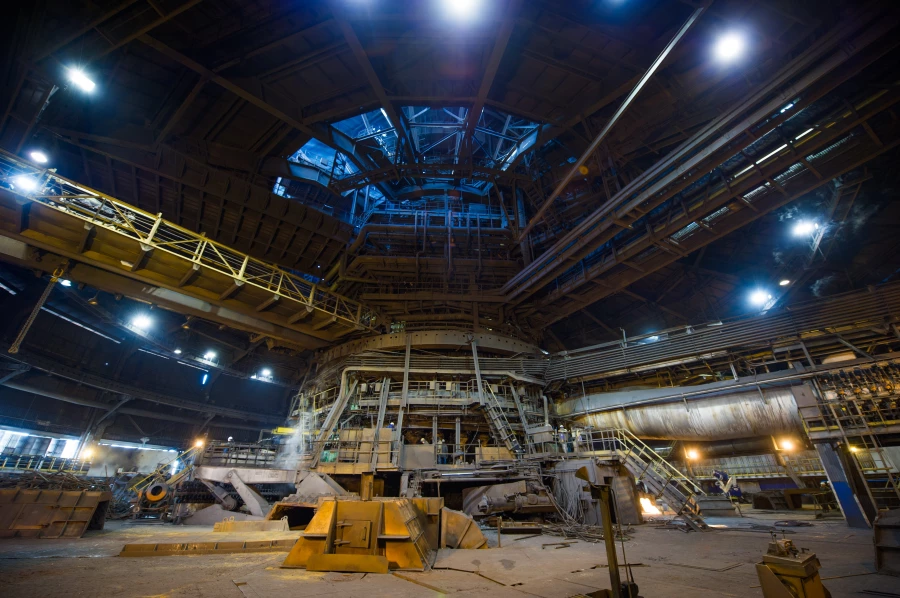
Доменная печь №5 иллюстративное фото: НЛМК.
Чтобы получить точное количество чугуна требуемого качества при минимальных топливно-энергетических затратах, важно рассчитать состав шихты и знать, и знать когда и в каком соотношении она попадет в печь. Основная сложность в том, что химический состав сырья постоянно меняется, а его поведение на участках шихтоподачи в бункерах неопределенно.
Раньше загрузка конкретного материала в печь определялась по приблизительным временным рамкам. Это мешало точно предсказать состав выходящего потока. Чтобы решить эту проблему на НЛМК внедрили цифровой сервис, который в режиме реального времени отслеживает движение сырья и его химический состав по всему тракту – от выгрузки до загрузки в доменную печь.
При создании сервиса использовали DEM-моделирование, которое позволило воспроизвести процесс перемешивания и предсказать, как будет изменяться состав на выходе. Эту модель совместили с еще одной – континуальной. В ее основе лежат математические формулы, описывающие физику поведения частиц.
Для подтверждения корректности данных, генерируемых математическими моделями, на НЛМК создали уменьшенный физический прототип стационарного бункера с прозрачными стенками. Именно он позволил открыть один из «черных ящиков» В итоге специалисты получили возможность наблюдать как ведет себя материал внутри бункера.
Далее начались эксперименты на реальном оборудовании с помощью технологии RFID – когда объект идентифицируется с помощью радиосигнала. Сырье с RFID-меткам загружалось вместе с основным потоком, метки считывались как на входе, так и на выходе. Дополнительно использовали лидар – он сканировал поверхность сырья в бункере.
Исследование показало, что фактическое движение сырья соответствует цифровым моделям.
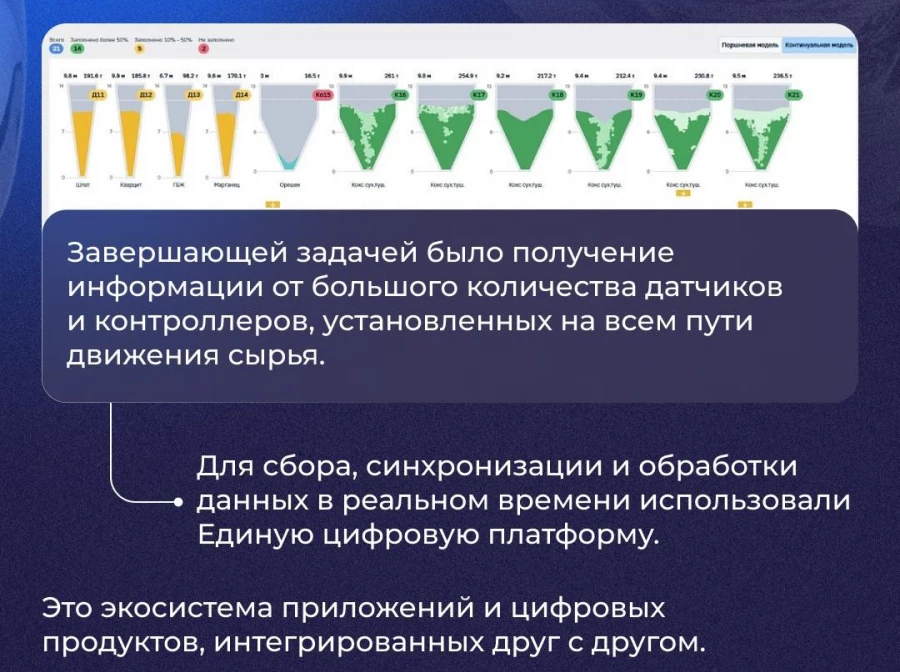