Сложная архитектура требует больших стеклопакетов — управляющий директор "Модерн гласс" Антон Войцехович
Один стеклопакет длиной 12 метров весит до 5 тонн, такие окна ставят на небоскрёбы и бизнес-центры. Раньше их делали только в Европе и Китае, теперь — в Челябинске. Завод «Модерн гласс» — единственный в России производитель крупноформатных стеклопакетов. Управляющий директор предприятия Антон Войцехович рассказал MASHNEWS, как перевозят стеклопакеты, какие компоненты не удалось импортозаместить и что мешает развитию крупноформатного остекления в России.
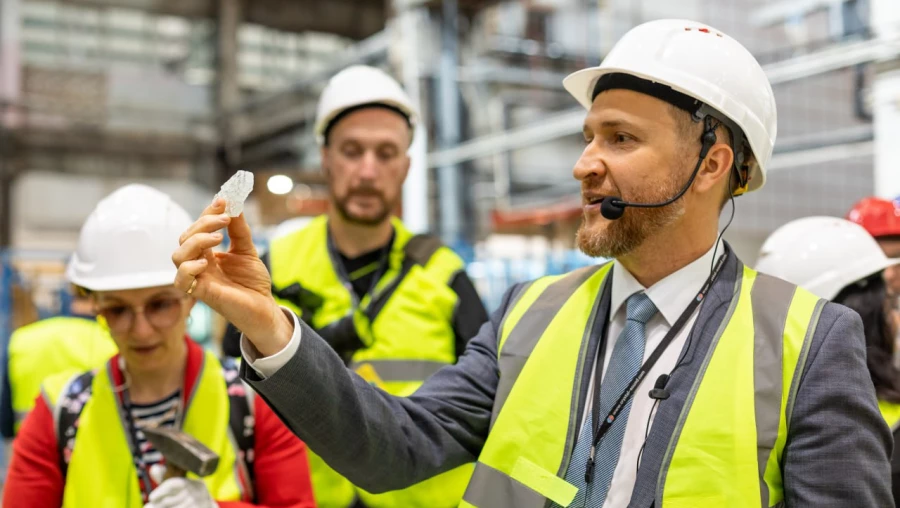
Гнутое стекло — в перспективе
— Ваш завод начал выпускать стеклопакеты длиной до 12 метров. Почему вы приняли такое решение?
— Это очень перспективное направление. Потенциал рынка крупноформатных стеклопакетов сложных форм огромный, так как Россия в архитектурном смысле примерно на 20–30 лет отстаёт от мировых лидеров. Для архитектуры размер фасадного стекла имеет чрезвычайно важное значение: большой формат даёт архитектору простор для творчества, постройка с таким остеклением смотрится весьма впечатляюще.
Иногда замысел архитектора бывает просто невозможно реализовать без определённого остекления. В некоторых случаях приходится идти на перепроектирование. Например, мы участвовали в проекте строительства штаб-квартиры РМК (Русской медной компании — ред.) в Екатеринбурге. Это здание известно как «Ананас» — внешне очень похоже. Архитекторы — Foster + Partners — перерабатывали проект специально под нас.
Заказчик хотел, чтобы всё стекло изготавливалось в России. Первоначально по проекту здесь должны были быть одиннадцатиметровые стеклопакеты, но в то время в России их никто не делал. И у нас тоже ещё не было соответствующего оборудования — объект начали строить в 2017 году. Поэтому здание было перепроектировано на шестиметровые изделия.
Сейчас мы единственная в России компания, которая выпускает крупноформатные стеклопакеты. Следующая цель — производить гнутое стекло. Такие изделия делают фасад очень необычным, впечатляющим. Скажем, такие конструкции использованы для зданий парка «Зарядье», в изогнутых фасадах «Лахта Центра». В России подобное стекло производят в размере только до 6 метров, и изогнуто оно только в одной плоскости. Остальные варианты — пока только импорт. Мы хотим освоить производство этой продукции.
— А раньше вы что производили?
— Мы начинали в 2002 году с производства перегородок для торговых центров. Потом купили оборудование для напыления и стали выпускать обычные стеклопакеты для жилых комплексов.
— Что такое напыление?
— Это нанесение специального покрытия, которое позволяет стеклу удерживать тепло, но при этом пропускает свет.
В 2006 году мы купили бывшую производственную площадку «Станкомаша» (завод, созданный в 1935 году, выпускал станки, во время Великой Отечественной войны — боеприпасы и башни для танков — прим. ред.) в Челябинске, к тому моменту здесь уже 20 лет ничего не производилось. Это здание, кстати, примечательно не только оборонным прошлым. Помните Чебаркульский метеорит?
— Тот, что упал в Челябинской области в феврале 2013 года?
— Именно. Мы в это время, около девяти утра, как раз сидели на совещании. Сначала увидели яркую вспышку, а через две минуты ударной волной у нашего завода снесло алюминиевый фасад. Мы все выбежали на улицу: думали, что автоклав взорвался. Слава богу, все остались живы.
— Значит, сначала вы не думали о производстве больших окон?
— В первое время делали обычные стеклопакеты и не планировали идти в сложную архитектуру. Да в России её тогда фактически и не было.
Сначала работали на региональном рынке. Например, мы делали стеклопакеты для нового здания Челябинского государственного краеведческого музея, для бизнес-центра «Высоцкий» и башни «Исеть» в Екатеринбурге, ещё для ряда проектов. Довольно быстро заняли почти половину местного рынка.
Но нам хотелось развиваться дальше, идти в более сложную архитектуру, так как рынок развивается, спрос на стеклопакеты нестандартного формата растёт. Поэтому в 2008 году мы вышли на московский рынок, на крупные стройки. Сейчас Москва занимает около 80% в объёме наших российских заказов. Наши стеклопакеты стоят в комплексе Neva Towers, «Острове мечты», деловом центре Matrix, концерном зале «Зарядье» и на многих других известных московских объектах.
Из Китая окно ждать долго
Фото: mos.ru
— До того, как вы стали делать 12-метровые стеклопакеты, откуда их поставляли в Россию?
— В основном из Европы, частично из Китая. Но в прошлом году в результате санкций поставки из Европы стали практически невозможны.
— И тогда вы решили, что пора действовать?
— Нет, такое решение мы приняли ещё до санкций, начали переговоры с Фондом развития промышленности о предоставлении кредита в размере 1,58 млрд рублей, общий объём инвестиций составил 2,2 млрд. Вы же понимаете, такие крупные проекты требуют довольно длительной и тщательной подготовки. Переоборудование производства — от идеи до ввода в эксплуатацию — заняло около двух лет.
У нас уже был опыт взаимодействия с фондом: мы брали в кредит 500 млн рублей на модернизацию производства. Ещё 500 млн рублей вложили сами. В результате мы нарастили производственные мощности на 25%, снизили потери сырья с 7% до 2%, освоили производство стеклопакетов длиной до 6 метров.
Со временем мы поняли, что готовы выйти на новый уровень — производить изделия вдвое больше по длине. Ведь импорт — довольно рискованный путь. Дело в том, что поставка из-за рубежа даже до санкций занимала месяцы. Если потребуется что-то оперативно изменить в проекте, приходится проходить множество этапов согласований, так как это иностранный контракт. Так что это не очень удобно для архитекторов, застройщиков.
К тому же если в ходе эксплуатации стеклопакет разобьётся, придётся долго ждать изготовления и поставки нового. Причём его необходимо заказывать именно у того производителя, который делал фасадное остекление на этом объекте, так как у другой компании характеристики стекла будут отличаться, и попасть в цвет будет практически невозможно. На фасаде это очень заметно.
Прошлогодние события показали, что мы были правы, когда решили выходить на новый размер. Например, мы узнали, что одни наши клиенты заказали в Европе стекло и из-за санкционных проблем ждали его больше года. Какой заказчик захочет так рисковать? Покупать в Китае — тоже не выход, всё равно доставка длится месяцами.
— Что вы купили на полтора миллиарда льготного займа ФРП?
— Мы закупили оборудование, которое позволяет перерабатывать стекло размером до 3,3 метра на 12 метров: технику для резки стекла, механической обработки, закалки, ламинирования, цифровой печати, изготовления стеклопакетов. То есть полный цикл производства крупноформатных стеклопакетов, которые мы теперь выпускаем под собственным брендом Hugesize.
До этого мы производили по 750 тыс. кв. метров стеклопакетов в год, перерабатывая 2,5 млн кв. метров стекла, то есть примерно 50 тыс. тонн — это как пять небоскрёбов «Москва сити». Благодаря реализации нового проекта мы нарастили наши мощности на 50%.
— Теперь импортировать крупноформатные стеклопакеты российским заказчикам не придётся?
— К концу 2024 года мы выйдем на проектную мощность — до 3,8 тыс. тонн в год — и сможем удовлетворить 90% российских потребностей в подобной продукции.
— Правильно я поняла: вы прекратили производство стеклопакетов для массового жилищного строительства?
— На данный момент наше приоритетное направление — проекты сложной архитектуры. Но совсем покидать массовый рынок не планируем. У нас есть действующее производство общестроительных стеклопакетов. Мы хотим его модернизировать для уральского рынка, где используется в основном простая архитектура. Окончательное решение пока не принято, поэтому рано говорить о сроках реализации. Сейчас у нас производство занимает 43 тыс. кв. метров плюс будет ещё 15 тыс. «квадратов».
Три джамбовоза на всю Россию
Фото: modernglass.ru
— Как вы доставляете такие большие стеклопакеты клиентам? По железной дороге?
— Когда мы были в начале пути, действительно думали развивать этот способ доставки. У нас есть собственная разработка специальных вагонов для перевозки, есть свои тепловозы. Но после пятилетней эксплуатации мы отказались от использования железной дороги. Автотранспортом быстрее и эффективнее: например, по железной дороге от Рязани до Челябинска продукция идёт 15–16 дней, а на машине — три дня.
Для транспортировки крупногабаритных стеклопакетов для нас на заказ в Германии изготовили три специальных прицепа — джамбовоза: один для изделий длиной 12 метров и два для девятиметровых. Это наша гордость, потому что в России таких джамбовозов больше нет. Стоимость каждого — примерно по 200 тыс. евро. Надеемся, что в России тоже научатся делать такие прицепы, так как рынок растёт, и трёх джамбовозов, конечно, мало. Всего же у нас задействовано 40–45 машин, около десяти машин в сутки выгружаются на заводе.
— На какое самое дальнее расстояние возили стеклопакеты?
— По земле — до 5 тыс. км. Наши изделия украшают здания Катара, Великобритании, Афганистана, Монголии, стран Балтии. Но у нас были заказчики и за океаном: несколько лет назад мы создали компанию в США, в Нью-Джерси. Сейчас из-за сложной геополитической ситуации и очень сложной логистики, к сожалению, мы не можем отгружать изделия в США. Хотя американский рынок очень привлекателен для нас.
— Неужели в Америке нет собственного производства крупных стеклопакетов?
— Представьте себе, нет! Максимальный размер, который они делают, — 6 метров, остальное завозят из Европы и Китая. При этом один только рынок стеклопакетов Нью-Йорка сопоставим с рынком России. Но сейчас он для нас закрыт. Как и Европа, где мы до 2022 года получили сертификаты, имеем опыт работы с лучшими европейскими компаниями. Например, мы работали с германской компанией Josef Gartner GmbH, которая входит в тройку мировых лидеров по производству фасадных конструкций. Так что наши компетенции позволяют нам работать на самом высоком уровне.
— Какова доля экспорта в ваших продажах?
— В 2022 году экспорт был примерно 30%. Мы продаём изделия в страны СНГ: Казахстан, Узбекистан, Киргизию, Белоруссию. Европа отвалилась, в Персидский залив мы пока не успеваем зайти, в Китае своих производителей достаточно. Так что пока это только постсоветское пространство.
— Кто сейчас мировой лидер на этом рынке?
— В Европе это германская компания Sedak. Но мировой лидер, конечно, Китай. Он очень быстро развивается, там делают гораздо более интересные и сложные вещи, чем в Европе.
Российская сода и иностранный герметик
Парк «Остров мечты». Фото: пресс-служба Комплекса градостроительной политики и строительства Москвы
— Вы говорите, что джамбовозы теперь за рубежом не купить. А оборудование для изготовления 12-метровых стеклопакетов тоже европейское? И оно тоже теперь недоступно?
— Да. И поэтому мы стараемся по максимуму переходить на отечественное оборудование, что-то производим сами. Например, системы подъёма — присоски — раньше покупали в Германии или Австрии, сейчас изготавливаем сами. С помощью челябинских заводов делаем металлическую раму, покупаем чашки присосок, компрессоры, трубки и собираем. То же самое с конвейерами: они тоже были австрийские и немецкие, теперь думаем самостоятельно производить это и другое базовое оборудование. Больше того, рассматриваем вопрос о том, чтобы наладить серийный выпуск.
— Стекло вы закупаете в России?
— Да, стекло отечественное. Нужное нам стекло поставляют в России только две компании: «Салаватстекло» (они производят прозрачное осветлённое стекло) и «Ларта глас» (стекло с напылением). Причём оба предприятия модернизировали свои мощности, чтобы выпускать стекло, подходящее для больших стеклопакетов сложной конфигурации.
Например, завод «Ларта глас» модернизировал установку для напыления, чтобы можно было работать со стеклом до 9,5 метра. Плюс они закупили специальное сырьё для изготовления осветлённого стекла. «Салаватстекло» переоборудовал мощности под производство осветлённого стекла и до конца 2023 года планирует завершить установку оборудования под выпуск стекла длиной до 12 метров.
Раньше такое стекло везли из Европы, в России его почти не делали. То есть получается, что мы создаём стимул для развития всей отрасли.
Следующий этап — полностью импортозаместить сырьё. Сейчас производители сырья используют российскую соду, но обогащённые пески не в полном объёме производятся в России. Их планировали закупать у Украины, но теперь это невозможно. Я знаю, что сейчас планируется возить из Израиля и Турции.
Часть оборудования начинают производить в России, например, моечное. Мы максимально настроены локализоваться, плюс собираемся перейти на российское программное обеспечение, сейчас оно австрийское.
— Что ещё пока не удаётся импортозаместить?
— Не так уж много позиций. Но они очень важные. Например, герметик в России не выпускают, мы покупаем его в Европе, а без него стеклопакеты произвести невозможно.
— Это мешает развитию?
— Да нет, вопрос решаемый. Вот что мешает, так это неготовность фасадных компаний развиваться. Для работы со сложными фасадными конструкциями, которые сейчас набирают популярность, нужно обучать персонал, приобретать специальное оборудование. Если производственные предприятия активно этим занимаются, то фасадные не очень.
Случается, что архитектор хочет сделать в проекте красивые крупноформатные стеклопакеты, но фасадчик говорит: я не подниму такое тяжёлое стекло, у меня нет оборудования. Ведь масса одного стеклопакета длиной 12 метров может доходить до 5 тонн. Бывает, что приходится менять проект, но, если архитектору важно, чтобы был именно задуманный формат, он настоит на своём.
Так было, например, с аэропортом Толмачёво в Новосибирске. Фасадная компания боялась, что не справится с двухтонными шестиметровыми стеклопакетами, которые предусмотрел архитектор, и предложила разбить их пополам, на трёхметровые. Архитектору удалось убедить фасадчиков, и аэропорт от этого только выиграл: крупные конструкции смотрятся гораздо интереснее.
Ещё одна проблема, которая создаёт неудобства, — дефицит кадров. Сейчас на нашем заводе работает 730 человек, открыто ещё около ста вакансий для работы на новом оборудовании. Их нужно набрать, потом обучить. Но найти людей всегда было очень непросто, а тут ещё мобилизация. Плюс оборонные предприятия пылесосят с рынка всё, что есть. Такие зарплаты, которые они обещают, неподъёмны для частного бизнеса.
— И как вы удерживаете персонал?
— У нас очень комфортные условия работы, на мой взгляд. Мы много внимания уделяем спорту: на заводе есть два тренажёрных зала, зал йоги, каждый день приходят тренеры, занятия для сотрудников бесплатные. Мы оплачиваем для них уроки танцев, вокала. Дважды в неделю на предприятие приходит медработник, с ним можно проконсультироваться насчёт вопросов по здоровью.
Ну и то, что мы постоянно развиваемся, — это тоже очень важно для наших сотрудников. Мы готовы вкладываться в подготовку специалистов. Стоимость обучения одного оператора доходит до 1 млн рублей.
СПРАВКА MASHNEWS:
Челябинское ООО «Модерн гласс» учреждено в 2002 году. По 45% долей в компании принадлежит Сергею Ванюкову и Михаилу Дедовичу, 10% — у Вячеслава Уварова. Выручка «Модерн гласс» в 2022 году составила 5,15 млрд рублей, чистая прибыль — 676,9 млн.
Окна производства «Модерн гласс» использованы для остекления фасадов концертного зала «Зарядье», тематического парка «Остров мечты», ТРЦ «Хорошо» в Москве, МФК Abu Dhabi Plaza в Астане, МДЦ Tashkent City в Ташкенте, ТРЦ Dordoi Plaza в Бишкеке — всего более 3500 объектов.