"Северсталь" привлекла к сотрудничеству искусственный интеллект
Благодаря цифровизации металлургической компании «Северсталь» удалось за пять лет на 55% повысить уровень качества производства. В этом помог Sherlock — система управления качеством продукции, которую разработали на предприятии.
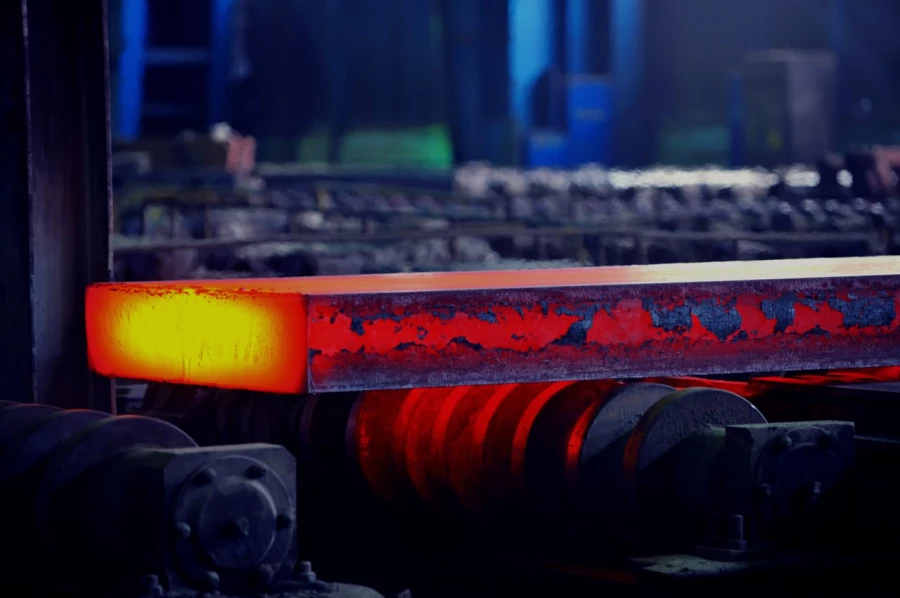
Вся информация в одном окне
О своих разработках в области искусственного интеллекта и внедрении их на производстве рассказал Пётр Мишнёв, директор по техническому развитию и качеству «Северстали». На вебинаре «Как цифровая система контроля качества продукции влияет на клиентский опыт», прошедшем 21 сентября, он сообщил, что благодаря внедрению цифровых технологий компании удалось существенно повысить качество продукции.
Это можно проиллюстрировать динамикой претензий от клиентов. Так, доля обращений, связанных с холодным прокатом, в 2018 году составляла 3,6% от всего объёма отгрузки, в 2022-м она снизилась до 0,7%. Доля обращений по поводу оцинкованного проката сократилась за тот же период с 3,1% до 1%. Всего за пять лет уровень претензий снизился на 55%.
Прежде чем начать работу по цифровизации управления качеством, специалисты компании проанализировали, какие именно процессы должны быть вовлечены в систему контроля. Металлургическое производство многостадийное, здесь задействовано большое количество параметров, правил для принятия решений о годности продукции. Традиционно российские металлургические предприятия этот объём информации не структурировали в единой базе данных. Информация была рассредоточена по различным источникам, её получали разными способами, причём не всегда формализованными, говорит Пётр Мишнёв.
«Когда 20 лет назад я пришёл после вуза на производство, то все параметры производства продукции нужно было переписывать вручную из бумажных паспортов качества. Это была норма в то время, и меня как молодого специалиста направили на эту работу: ходить по цехам, искать документы и выписывать показатели», — рассказывает он.
Большинство предприятий и сегодня недалеко ушли от такой системы. Это отнимает много времени, к тому же сотруднику не всегда доступна полная информация, которая ему необходима для принятия решений.
«Мы решили вооружить сотрудников такими инструментами, которые помогли бы им объективно оценить ситуацию, чтобы принимать решения на основе фактов, измеренных объективными цифровыми помощниками», — поясняет Пётр Мишнёв.
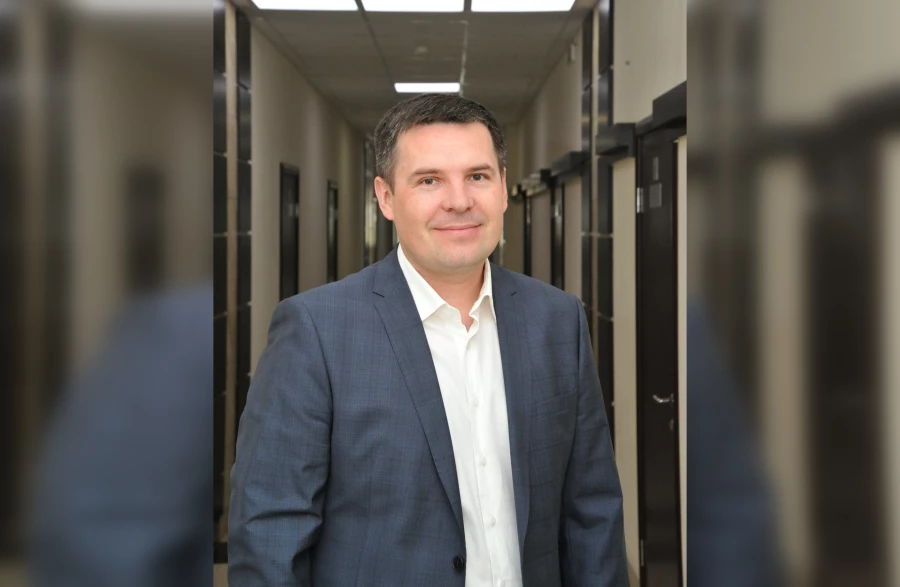
Контроль на четырёх «китах»
Внедряемая на предприятии система управления качеством продукции состоит из четырёх элементов.
Первый — это цифровые измерители. Их главная задача — зафиксировать состояние поверхности, формы металла и выделить отклонение от стандарта. Человеческий глаз не способен конкурировать со специальной видеокамерой: человек устаёт, он вынужден отвлекаться, его внимание не всегда постоянно. Иногда глаз попросту не способен уследить за поверхностью, ведь на производстве есть операции, где полоса металла движется со скоростью 25 м/с и больше.
«Наши специалисты готовы разрабатывать и поставлять внешним клиентам такие системы измерения в потоке», — говорит Пётр Мишнёв.
Второй элемент — прогнозная модель, которая способна по определённым показателям предсказать наличие дефектов, находящихся внутри полосы металла. Ни глаз, ни камера не могут увидеть такой дефект, а его наличие может оказаться критически важным. Например, если при штамповке капота или крыши автомобиля в составе металла будут посторонние включения размером всего несколько микрон, то это может привести к порыву в тех местах, где происходит наибольшая вытяжка металла.
«Элементы прогнозирования используются примерно на половине наших производственных переделов. Мы на этом не останавливаемся и стремимся наращивать долю переделов, оснащенных этой системой», — отмечает Пётр Мишнёв.
Третья составляющая — система слежения за металлом. Это программное обеспечение, которое фиксирует местонахождение продукта по узлам агрегата в каждую единицу времени. Она нужна, чтобы к продукту мы могли привязать снятые измерителями данные и впоследствии знать, откуда надо вырезать бракованный участок.
И четвёртый элемент — система автоаттестации. Она выдаёт человеку решение о том, отгружать ли рулон дальше (в этом случае загорается зелёный светофор), нужно ли его проверить и на что именно стоит обратить внимание (жёлтый). Либо если отклонение критично, то загорается красный свет, и продукция отправляется в брак.
Интеллект — как у сыщика
Система управления качеством имеет собственное имя — Sherlock. Аналогия понятна: как знаменитый сыщик, она способна найти и предоставить сотруднику информацию о том или ином продукте. Причём она выдаст все данные, которые позволят человеку принять решение, касающееся этого продукта. Например, по запросу он получает данные, насколько критична частота отклонения интересующего его показателя; если отклонение находится на некотором расстоянии от кромки, является ли это вариантом нормы.
Sherlock аккумулирует аналитику о количестве продукции с отклонениями, частоте выявления таких отклонений, о видах встречающихся дефектов. На основе этих данных можно автоматизировать механизм принятия решений о назначении той или иной продукции. Например, для одного назначения тот или иной показатель критичен, как неметаллические включения для крыши автомобиля. А для другого — скажем, для профилей, из которых делают ограду — такое допустимо.
«Работы по проекту начали в 2017году, а в 2018 году уже был разработан Прототип системы Sherlock вместе с одной французской компанией. Позже при поддержке другой компании мы полностью переделали данное решение и перешли на собственную разработку. Sherlock мы также готовы разработать для других предприятий и установить на их объектах», — говорит Пётр Мишнёв.
Внедрение Sherlock длится уже семь лет, в 2026-2028 годах «Северсталь» рассчитывает охватить ею 80% производственных переделов. Более широкий охват неэффективен с точки зрения инвестиций, поясняет Пётр Мишнёв. Вложения в этот проект уже составили 1,28 млрд рублей, в общей сложности они вырастут до 2,5-3,5 млрд.
Реализует инициативы команда экспертов «Северстали», обладающих необходимыми компетенциями, из дирекции по техническому развитию и качеству, производственных подразделений Череповецкого металлургического комбината, а также профильных компаний – «Северсталь Диджитал» и «Северсталь-инфоком».
Система Sherlock установлена на 16 крупных агрегатах на производстве, через неё проходит 4,2 млн тонн товарной продукции из общего объёма 10,7 млн тонн.
Кроме того:
- 9 агрегатов оснащены системами инспекции поверхности;
- 15 — системами контроля по геометрии;
- 8 — системами слежения за металлом;
- 7 — системами контроля инцидентов.
Внедрение системы управления качеством обеспечивает:
- снижение потерь благодаря повышению базового качества продукции;
- скорость реакции на обнаружение дефектов;
- поставку точно в срок благодаря выявлению отклонений на ранних стадиях производства продукции;
- гарантию качества на 100% длины продукта за счёт непрерывных измерительных систем и минимизации человеческого фактора.
Примеры улучшения клиентского опыта
Металлопрокат для коммерческих транспортных средств. Автоматизирован алгоритм проверки допусков по толщине на горячекатаном прокате, а также построена модель логистической регрессии для формирования прогноза появления дефекта на слябе. Эти меры позволили избежать ошибок на этапе приема заказов, связанных с человеческим фактором.
Штрипс для нефтегазопроводных труб. Введен в работу серпомер на стане горячей прокатки для оценки величины серпа на рулоне. Для ряда клиентов, заказывающих рулон для изготовления штрипса, это позволило избежать отсортировки.
Инструменты будущего
«Мы единственная компания в металлургической отрасли России, которая внедряет такую комплексную систему сквозной автоматической аттестации продукции по всем переделам. Цифровые помощники, используемые нашими конкурентами, направлены на решение отдельных задач: снижение затрат на производство, отслеживание качества на некоторых переделах. Но комплексно этим пока не занимаются. Между тем в современных конкурентных условиях качество продукции имеет определяющее значение», — констатирует Пётр Мишнёв.
На ближайшее будущее предприятие ставит задачу максимально вовлечь сотрудников в систему управления качеством: несмотря на огромную роль цифровых инструментов, без участия человека не обойтись. Есть проблемы, которые цифровые помощники не фиксируют. Сообщая о подобных проблемах и внося их в базу данных, сотрудники помогают совершенствовать систему, чтобы ещё существеннее повысить качество работы предприятия.
В перспективе «Северсталь» рассчитывает по максимуму определить все критичные параметры, влияющие на качество, и внести их в цифровую систему. А потом, вооружившись этой полной картиной, искусственный интеллект, возможно, будет сам принимать решения о том, какую технологию выбрать и как аттестовать продукцию — как годную или брак. Это, конечно, довольно отдалённое будущее, но 20 лет назад современные цифровые системы тоже выглядели как что-то из области фантастики. Теперь же эти цифровые инструменты — must have для современного эффективного предприятия, резюмирует спикер.