Пилим, сушим, продаем: российский леспром держится на импортных станках и локальных брендах
В Архангельской области разработали первую российскую харвестерную головку - это основное рабочее устройство лесозаготовительных машин. Проект может стать успешным, наряду с другими такими локальными инициативами он частично решит проблему серьезной зависимости лесопромышленного комплекса страны от зарубежных технологий.
Mashnews выяснил, почему импортозамещение средств производства в леспроме идет недостаточно быстро, и как удается держаться на плаву немногим пионерам отрасли.
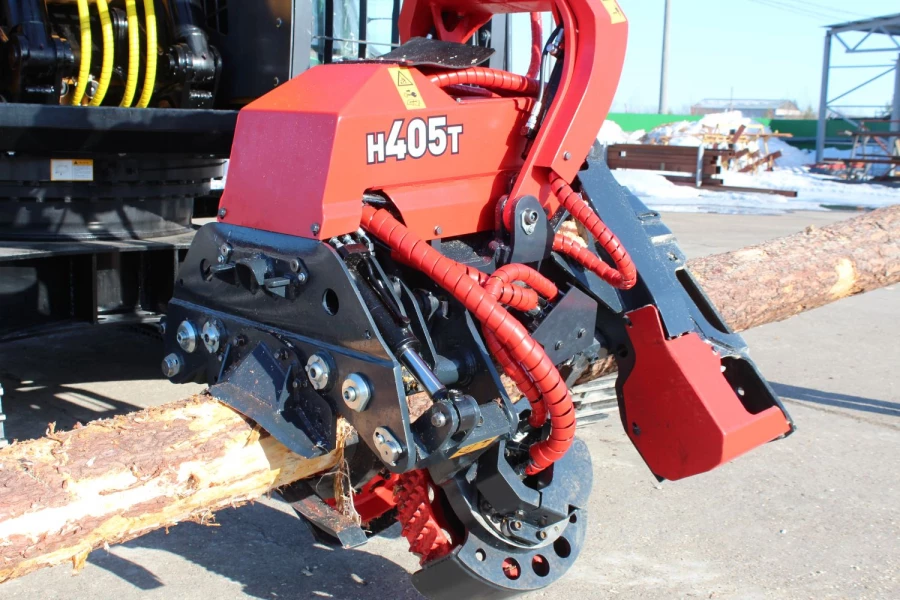
Архангельские разработки
О разработке харвестерной головки на встрече с президентом России Владимиром Путиным 11 марта рассказал губернатор Архангельской области Александр Цыбульский.
«Никогда – думаю, не ошибаюсь, – в истории мы не делали собственных харвестерных головок. Мы ее полностью разработали, мы ее полностью сделали. Наши архангельские ребята...», - сказал Цыбульский.
Харвестерная головка, которой присвоили название Logger H405, будет выпускаться архангельской компанией «Арктик Индастри». Помимо нее, инженеры предприятия разработали систему измерения и управления головой – Logger Rite. Испытания харвестерной головки начались еще в 2023 году.
Уже в этом апреле, по словам губернатора, заработает цех, который будет выпускать до 80 головок в год. С перспективой увеличения объема производства до 200 головок в год.
«Фактически мы сможем почти полностью годовое потребление такой техники для нашего леса обеспечить», - сказал Цыбульский.
Три года тишины
Практически все ведущие мировые поставщики оборудования и режущего инструмента для леспрома ушли с российского рынка после февраля 2022 года и введения санкций. Исключение составили единицы итальянских, чешских, южнокорейских фирм, но им пришлось поменять вывески и представляться теперь отечественными производителями.
Запасные части и некоторый режущий инструмент по возможности перешли в «серый» импорт. Однако многие европейцы прекратили даже такие поставки, так как оборудование номерное, и при любом запросе из России был ответ: «не обслуживаем, не работаем – санкции».
Особенно остро встал вопрос по лесопильному и мебельному оборудованию, производству столярно-строительных конструкций, аспирации, компрессорному оборудованию. Одним из немногих вариантов стали поставки с китайских фабрик, принадлежащих бывшим европейским партнерам. Появились техника и технологии из Турции и Индии.
Многие наши лесопромышленники привыкли работать на европейском оборудовании, то есть в России достаточно искушенные и в известном смысле избалованные пользователи. От азиатских и российских станкостроителей они ждут того же функционала, возможностей, качества, которое ранее обеспечивали финны, немцы, австрийцы, американцы.
Отечественные предложения такого уровня появляются, но происходит это не такими темпами и не в тех масштабах, чтобы можно было говорить о начавшемся полноценном процессе импортозамещения.
Наш ответ Чемберлену
Помимо альтернативных импортных поставок кое-что начали делать и в России, в том числе писать свое ПО для импортных станков, наладили реверс-инжиниринг самых востребованных запчастей, но пока это локальные успехи, которые в основном держатся на энтузиазме участников проектов.
Лучше других преуспели те, кто начал работать лет 10-15 назад, приобрел необходимые компетенции и запустился в сравнительно хороших экономических условиях.
«Наше предприятие выпускает режущий инструмент почти 10 лет под своей маркой GT. Раньше мы занимались поставками импортного инструмента и его сервисным обслуживанием, а уже в 2016 году на базе станочного парка сервисного центра было запущено собственное производство. На сегодняшний день мы выпускаем всю ассортиментную линейку, требующуюся леспрому, – от инструмента для лесопиления до производства мебели и напольных покрытий. В ассортименте компании сейчас более 1000 позиций», - рассказывает заместитель технического директора петербургской компании GT Владимир Падерин.
По данным эксперта, основную часть отечественного оборудования и инструментов для лесопромышленного комплекса выпускают как раз старожилы отрасли. Они занимают долю около 10% рынка. Специалисты знают эти фирмы наперечет. А вот перспективы производителей, которые находятся в самом начале пути, весьма туманны.
Еще один пример успеха в узком сегменте – компания Remdrev, которая начала делать сушильное оборудование в Вологде еще в 2019 году. Отечественные аналоги дешевле зарубежных агрегатов на 20-50%, а их поставки и обслуживание стабильны, не подвержены влиянию внешней конъюнктуры.
«За последние три года произошла практически полная локализация производства комплектующих для наших сушильных камер. Сейчас оборудование не уступает по уровню импортному, среди наших заказчиков есть крупные отраслевые компании, а они знают толк в хорошей технике. Приспосабливаемся, стараемся удовлетворить высокий запрос по работе автоматики и специфическим комплектациям. Серьезные требования клиентов подталкивают нас к развитию, мы справляемся», - рассказал генеральный директор Remdrev Артем Лукичёв.
Компания привлекла к сотрудничеству других российских машиностроителей, в частности, завод электродвигателей «Уралэлектро» из Оренбургской области. Его продукцией заместили итальянские движки Lafert, модернизировали и адаптировали некоторые элементы, оборудование со своей задачей успешно справляется.
Нужен компетентный покупатель
Своей оценкой темпов импортозамещения поделился с Mashnews руководитель Ассоциации производителей машин и оборудования лесопромышленного комплекса, доктор технических наук Александр Тамби. Как отмечает эксперт, отрасль за все время санкций не смогла именно в деревообработке заместить основные станки.
В лесопилении это высокоскоростные станки для распиловки бревен, в фанерном производстве – оборудование для лущения шпона, в плитном производстве – прессы, вокруг которых строится технологический процесс. И даже в разрезе биотоплива появившееся отечественное оборудование пока имеет невысокую производительность, но оно есть.
«Ведущие мировые производители обладают большим опытом, исчисляемым десятилетиями, у них было время на отработку и доводку всех технологий. У наших компаний-производителей оборудования для леспрома такого опыта нет. Есть желание разработать, уже есть готовые решения, умы и руки, но, к сожалению, нет потребителя» - констатирует Александр Тамби.
По словам эксперта, за время санкционных ограничений не получилось практически ни в одной подотрасли деревообработки сформировать пул хотя бы из десяти заказчиков, которые были бы готовы заказать однотипные скоростные станки у отечественных производителей. Делать партиями меньше – бессмысленно, машиностроительный проект никогда не окупится. Нужен выход в тираж, массовый заказ, возможно, даже с выходом на экспорт.
Еще один важный фактор – привычка к очень низкой рентабельности деревообработки. При этом в секторе пиломатериалов денежный оборот самый большой. Сейчас производители просят разрешить им продавать пиломатериалы естественной влажности, то есть пока не готовы вкладываться даже в сушку древесины. Но есть желание купить высокопроизводительное импортное оборудование, чтобы зарабатывать на объемах производства продукции с низкой добавленной стоимостью.
Намного лучше ситуация в целлюлозно-бумажной промышленности, где нашли технические решения по замене западного оборудования на аналоги, внедрили собственные разработки, в том числе ПО. Там больше уровень производственной культуры, больше глубина переработки и добавленная стоимость конечного продукта, лучше экономика и перспективы, даже в условиях технологического сдерживания.
Где искать решения
«Импортозависимость никуда не денется, наверное, в ближайшие десятилетия по той причине, что мы сами себе не готовы верить, что мы сможем от этой зависимости избавиться и сделать что-то сами. Должны пройти глубокие изменения в психологии потребителя. Рентабельность отрасли сильно снизилась из-за закрытия западных рынков, и сегодня очень многие предприятия не вкладываются в развитие», - сетует Александр Тамби.
Тем не менее внутренний спрос на отечественные разработки понемногу растет. Среди ключевых трудностей – разобщенность участников отрасли, особенно лесопильщиков. Отсутствует единая позиция по большинству оргвопросов, включая системное обеспечение ЛПК техникой и технологиями. Только начинается налаживание контактов между производителями оборудования для леспрома и его покупателями.
Таким образом, пока нет возможности четко сформулировать и запрос к государству по мерам поддержки в разрезе технологического развития. Эксперты рассчитывают на расширение диалога всех участников, чтобы достичь синергетического эффекта в смежных и взаимозависимых отраслях.