Нечем крыть. Нефтяники могут снизить требования к защите от коррозии
Производители материалов для борьбы с коррозией перешли на китайские компоненты, которые «не дотягивают» до европейских. Например, с их помощью нельзя создать высокотемпературные покрытия для нефтепроводов. Из-за этого ВИНКи могут пересмотреть свои стандарты и требования к поставщикам.
В России нет собственного производства эпоксидной смолы, которая служит основой для антикоррозионных материалов. До 2022 года сырьевые компоненты для нее поставлялись из западных стран, сегодня – из Китая. Однако азиатские аналоги не позволяют создавать высокотемпературные покрытия, которые необходимы, например, для работы с некоторыми видами нефти.
Проблема разработки новых отечественных материалов и технологий стала одной из ключевых тем 27-й Международной выставки-конгресса «Защита от коррозии» в Санкт-Петербурге. Как стало известно Mashnews, в отсутствии доступных решений на рынке крупные энергетические компании уже рассматривают возможность изменения своих внутренних стандартов за счет снижения антикоррозионных требований. Но вот вопрос: как это скажется на надежности и долговечности новых трубопроводов.
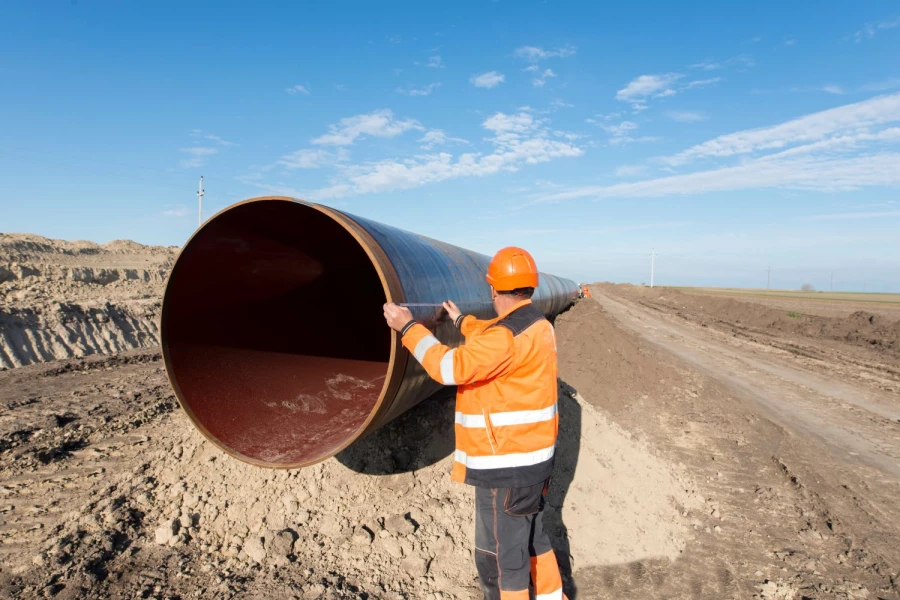
Китайское сырье выручает, но нужно свое
Ущерб от коррозии достигает 3–5% мирового ВВП, а потери металла в результате разрушительных процессов оцениваются в 20%. Поэтому компании постоянно находятся в поиске эффективных материалов и технологий для защиты конструкций от коррозии. Особенно остро этот вопрос стоит в нефтегазовой промышленности, где оборудование работает в условиях агрессивных сред и экстремальных температур.
В 2022 году с рынка ушли многие производители антикоррозионных материалов из США, Германии и других западных стран, освободив место для российских поставщиков. Но одновременно исчезло и европейское сырье, которое использовали отечественные заводы. Возить компоненты начали из Китая, Южной Кореи, Индии.
«В ряде случаев это привело к временному ухудшению качества или изменению рецептур, но многие производители адаптировались, находя альтернативные решения», - рассказал Mashnews Павел Абатуров, коммерческий директор Научно-производственного холдинга «ВМП» - группы компаний, занимающейся разработкой и производством защитных покрытий для различных отраслей промышленности.
Тем не менее, даже хорошие материалы могут дать сбой из-за сырьевых изменений. «Из-за замены импортных компонентов, изменения рецептур и роста доли «упрощенных» решений покрытия могут требовать повышенного внимания к состоянию защищаемых конструкций», - пояснил Павел Абатуров.
Исчезновение европейских добавок стало серьезной проблемой для рынка, но сегодня в большинстве случаев замена им найдена, сообщил генеральный директор лакокрасочного завода АО «КРОНОС СПб» Владимир Калачев. Он добавил, что предприятие не снизило объемы производства, а качество готовых антикоррозионных ЛКМ на китайском сырье не уступает европейским образцам.
Однако некоторые высокотемпературные виды покрытий создать с помощью китайских компонентов нельзя. Так, европейское сырье до 2022 года позволяло получать покрытия, выдерживающие температуры до 150°C, а доступные сегодня азиатские аналоги рассчитаны на среды максимум до 130°C. Поэтому в России нужно как можно скорее запускать собственное производство эпоксидных смол (основа для создания защитных покрытий) – и именно на отечественном сырье, подчеркнула заведующая лабораторией защитных покрытий и полимерных функциональных материалов ООО «Исследовательский центр ТМК» Юлия Прыкина.
«Самая опасная ситуация – с эпоксидами. Потому что это не только трубная отрасль, это и судо-, и авиастроение, и клеи. А в нашей стране эпихлоргидрин и бисфенол А (базовые компоненты для получения эпоксидных смол – прим. ред.) теперь не синтезируются вообще. Они уже давно завозятся в Россию, хотя раньше у нас были свои крупные заводы», - прокомментировала эксперт.
Она добавила, что выпуск эпоксидных смол – дорогое, сложное и очень вредное производство, которое вряд ли смогут освоить небольшие компании без серьезной господдержки. В то же время крупным химическим холдингам это направление не так интересно из-за относительно небольших объемов потребления.
СПРАВКА MASHNEWS
- Материалы на основе эпоксидной смолы применяются в строительстве и производстве для обеспечения защиты от агрессивной химии, механического износа, коррозии. Эпоксидные смолы выпускались в СССР, на производственные мощности которого приходилось около 10% мирового объема. В 2000-е годы большинство производств было закрыто. Также было ликвидировано и последнее на территории России производство эпихлоргидрина – базового сырья для эпоксидной смолы.
- В декабре 2024 года компания «Полипласт-УралСиб» объявила о начале работ по проекту производства эпоксидных смол в рамках нацпроекта «Новые материалы и химия». Завершение строительства и ввод новых мощностей запланированы на первый квартал 2026 года. В конце 2023 года стало известно, что холдинг «Росхим» включил в проект Федерального центра химии в Усолье-Сибирском производство эпихлоргидрина, а затем и самой эпоксидной смолы. Также группа компаний «Титан» заявляла о планах запустить новый завод эпоксидных смол по собственной технологии к 2027 году.
Нефтегаз задает планку
Переход с европейского сырья на китайское однозначно сказался на качестве антикоррозионной защиты, в том числе в нефтегазовой промышленности, считает исполнительный директор Ассоциации содействия в реализации инновационных программ в области противокоррозионной защиты и технической диагностики (СОПКОР) Николай Петров.
«Далеко не все покрытия с использованием материалов на основе китайских ингредиентов могут обеспечить те параметры, которые были изначально заложены в ТУ и стандартах покупателя», - пояснил глава СОПКОР.
Крупные компании – такие, как «Газпром» или «Транснефть», всегда отличались высокими требованиями к качеству покрытий, которым в нынешних условиях стало сложно соответствовать. Как рассказали Mashnews два источника в отрасли на условиях анонимности, сейчас российские вертикально интегрированные нефтяные компании (ВИНКи) рассматривают возможность снижения требований к антикоррозионным покрытиям, поскольку отечественные поставщики в отсутствии нужного сырья не могут обеспечить выполнение внутренних стандартов компаний. Прежде всего, речь идет о защитных покрытиях газо- и нефтепроводов.
«В свое время один из крупных заказчиков поставил нам задачу создать покрытие, выдерживающее температуру +80°C, что необходимо для работы с определенными видами нефти, и мы его сделали. А есть покрытия, где мы даже не стали участвовать, потому что понимали, что не сможем справиться с этой задачей – нет всех компонентов, которые должны были бы присутствовать в рецептуре такого материала», - рассказал руководитель АО «КРОНОС СПб» Владимир Калачев.
В то же время, по его мнению, высокие требования стимулируют производителей антикоррозионных лакокрасочных материалов (ЛКМ) создавать новые, более эффективные решения, поэтому снижать планку нежелательно. В моменте такой шаг, может, и облегчит жизнь обеим сторонам, но в перспективе не поспособствует развитию.
«У китайцев еще 20 лет назад никакой химической промышленности не было, а сейчас они готовы поставлять все, что угодно, из того, что мы производим в России, и по более низким ценам. Таким образом они уже душат российского производителя сырья», - подчеркнул Владимир Калачев.
Он добавил, что петербургский завод сейчас разрабатывает новые функциональные добавки в материалы для борьбы с коррозией, чтобы заместить китайские компоненты в рецептурах.
Не снижать требования, а управлять рисками
Участники рынка уверены, что энергетические компании все-таки не пойдут на серьезное снижение требований к антикоррозионной защите.
«Трубопровод покрывается специальным составом изнутри, чтобы не было коррозии, и если температурный режим покрытия будет ниже предусмотренных требований, это скажется на долговечности объекта. Но пока компании на такое снижение не идут. Они тоже понимают, что, если где-то на севере проложить трубопровод, он должен служить запланированное количество лет, и никто не будет ремонтировать его каждые 2-3 года – это очень дорого и сложно из-за природных условий», - пояснил Владимир Калачев.
Трубные и нефтегазовые компании, наоборот, ужесточают свои требования к покрытиям, поскольку условия добычи энергоресурсов только усложняются, подчеркнула Юлия Прыкина. А производители антикоррозионных ЛКМ ищут решения, чтобы удовлетворить потребности своих заказчиков.
По словам Павла Абатурова, в нефтегазовой, энергетической и химической отраслях требования остаются жесткими, чтобы максимально минимизировать технические (ускоренная коррозия, сокращение межремонтных интервалов), экономические (экономия на материалах оборачивается частыми ремонтами, увеличение страховых выплат), репутационные и экологические риски.
«Требования не столько снижаются, сколько трансформируются в сторону управляемых рисков. Происходит некоторый рост затрат на тестирование материалов перед применением и усиление контроля на этапе нанесения», - добавил коммерческий директор НПХ «ВМП».
Он подчеркнул, что некоторые российские производители уже много лет предлагают высококачественные защитные покрытия со сроком службы до 30 лет, в том числе в сложных климатических условиях арктических месторождений и морских платформ.
«На российском рынке есть компании-производители антикоррозионных материалов, продукция которых соответствует мировым стандартам качества. Однако для дальнейшего укрепления позиций российских производителей и ускорения процесса внедрения инноваций необходима синхронная работа государства, бизнеса и науки. В том числе дополнительные меры государственной поддержки, чтобы способствовать развитию химической отрасли в выпуске необходимых сырьевых компонентов», - заключил Павел Абатуров.
В ПАО «Транснефть» запрос Mashnews о возможных изменениях
требований к защите от коррозии оставили без ответа.