ГУП «ТЭК СПб» стало первым в России теплоэнергетическим предприятием, внедрившим 3D-печать для выпуска деталей
Пилотный проект по производству запчастей посредством аддитивных технологий стартовал осенью прошлого года.
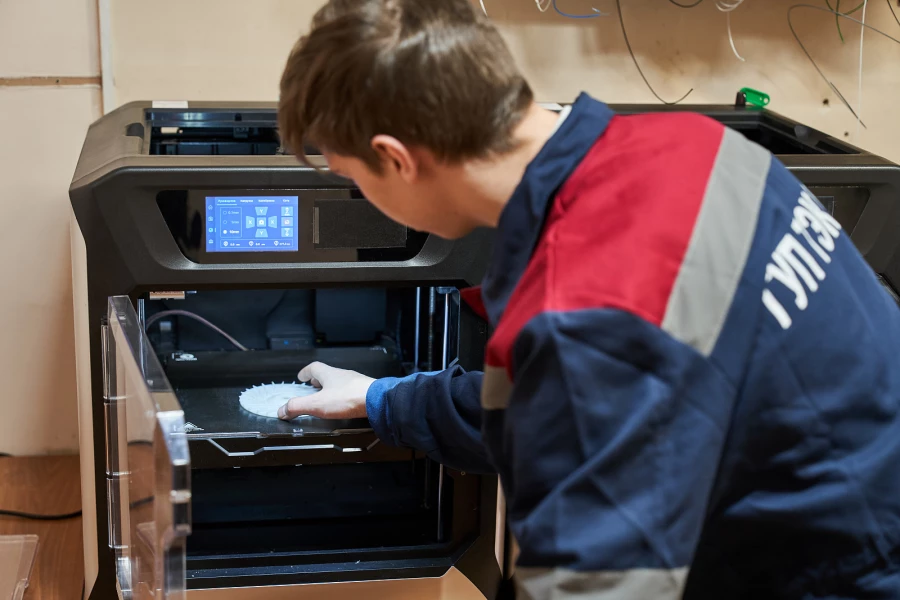
Фото: ГУП «ТЭК СПб».
Сегодня 3D-принтеры позволяют петербургским теплоэнергетикам создавать снятые с производства и недоступные импортные запасные части, менять их вне целого комплекта, а также избегать простоя оборудования.
За год на предприятии произвели более 210 единиц продукции 49 наименований. Среди выпускаемых деталей – механические комплектующие для автоматических горелок, крыльчатки охлаждения, торцевые уплотнения, уплотнительные кольца для насосов и другие запчасти.
Применение аддитивных технологий для нас – не только очередной шаг к локализации и импортозамещению, рассказал генеральный директор ГУП «ТЭК СПб» Иван Болтенков.
«Мы наращиваем скорость ремонта, минимизируем зависимость от поставщиков и непредсказуемой логистики, исключаем ненужные траты. Так, в прошлом поломка крыльчатки охлаждения требовала замены целого насоса. Теперь же достаточно напечатать и установить новую деталь – за год 3D-печать позволила нам сохранить порядка 20 единиц такого оборудования. Запчасти подтвердили свою надежность при длительной эксплуатации».
Фото: ГУП «ТЭК СПб».
При производстве деталей с помощью 3D-принтеров специалисты ГУП «ТЭК СПб» прибегают к реверс-инжинирингу – создают все запасные части с нуля.
Эскизы строятся на основе ранее изготовленных, старых, а иногда и сломанных запчастей. Затем разрабатывается 3D-модель, которая загружается в специальную программу. Для печати необходимо задать до 600 параметров – каждый из них, как и материал для печати, подбирается под конкретную деталь. Принтер работает со скоростью 600 мм/сек, а печать занимает от 20 минут до нескольких часов. Так, порядка 16 часов ушло на производство крыльчатки охлаждения диаметром 35 сантиметров. Деталь успешно эксплуатируется на Приморской котельной.
В общей сложности использование 3D-печати позволило оперативно и своевременно произвести ремонт на источниках, в зоне работы которых проживает почти полмиллиона потребителей – от котельных зависит теплоснабжение свыше 1940 зданий, в том числе более 980 жилых домов, а также 170 детских садов, школ, больниц и других социальных учреждений.