Станки договорятся. Автопроизводители переходят на онлайн-контроль продукции
На елабужском заводе группы «Соллерс», где выпускаются легкие коммерческие автомобили, установили программный комплекс онлайн-контроля за производством. Вложения велики, но в итоге должны привести к экономии средств. Это не первая ласточка в российской автопромышленности. Без искусственного интеллекта и тут не обходится, выяснил Mashnews.
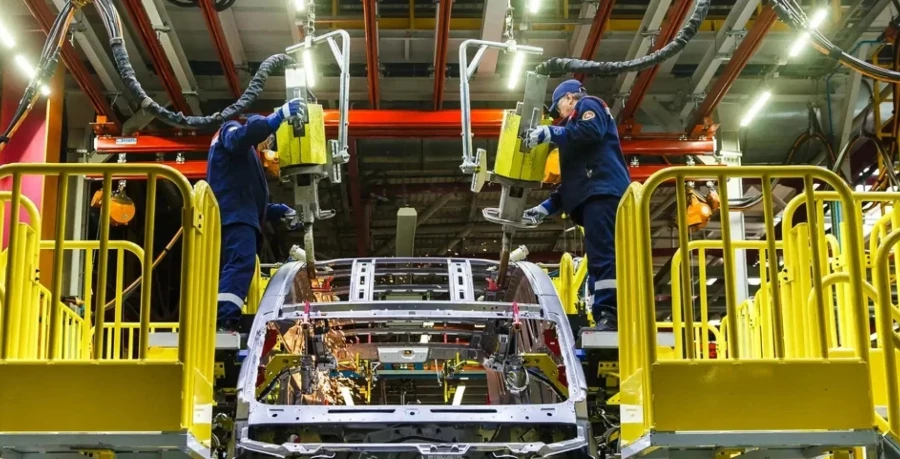
Сразу удалось сократить простои
На елабужском заводе компании «Соллерс» начал работать программный комплекс онлайн-контроля за работой промышленного оборудования. Это отечественная разработка под названием WINNUM, внедрением занимался промышленный интегратор PROF-IT Group. Платформа основана на технологиях IoT и Big Data, а суть работы сводится к следующему: со 160 единиц оборудования, включая металлообрабатывающие станки и сборочные станции, каждые несколько секунд считывается информация, которая позволяет оценить состояние инструментов. Но не только.
По словам руководителя PR-департамента ПАО «Соллерс» Алины Комаровой, комплекс полностью автоматизирует учет сырья, выпуска продукции и формирование отчетности, также он должен «повысить эффективность производства в целом за счет предиктивной аналитики и исключения ручного труда».
Что касается ответа на вопрос «почему Елабуга», а не какое-то другое производство группы, то в «Соллерс» поясняют: выбор пал на этот завод благодаря очень высокому уровню его автоматизации.
«С первого этапа система начала приносить ощутимые результаты: удалось существенно сократить незапланированные простои оборудования за счет раннего выявления отклонений в работе машин и механизмов», - рассказывает Виктория Чирва, руководитель направления внешних коммуникаций PROF-IT Group.
Одним из ключевых эффектов, по ее словам, стала возможность избавиться от такого явления как «бутылочные горлышки» на производстве. Система показывает, где происходит замедление, а также помогает выявить причины возникновения сбоев.
Стоимость? Конечно, коммерческая тайна, сказали нам в компании-разработчике. А в пресс-службе компании-интегратора пояснили: «Бюджет подобных проектов исчисляется десятками миллионов рублей, это соответствует средней стоимости аналогичных проектов на рынке. Конечная цена определяется объемом, требованиями к функционалу, интеграции и отчетности».
Не сенсация, а задел на будущее
Новинка от «Соллерс» интересная, однако сенсационной ее не назвать – подобные решения внедряют и другие отечественные производители. Для мелких производств это дорого и в какой-то степени бессмысленно, говорит генеральный директор компании «Механика» Дмитрий Даньшов.
С ним согласен и технолог опытного производства химических источников тока компании АО «АВЭКС» Андрей Корчун: «Такой подход используется на высокотехнологичных производствах, он однозначно улучшает и упрощает процесс контроля, убирает человеческий фактор, насколько это возможно. Однако начальные вложения велики, и не каждый производитель будет рассматривать такой вариант контроля, предпочитая ему человеческий труд».
По словам эксперта, о малых предприятиях в данном случае можно говорить, только если это «ультра hi-tech», но в таком случае и «масштабы обычно немалые». Буквально несколько примеров: «Технониколь», крупный производитель стройматериалов, используют систему контроля за состоянием оборудования, а вот «Тулажелдормаш» - нет, так как с продукцией в виде 10-18 поездов в год им это просто не нужно, отмечает Даньшов.
Автомобильные предприятия не исключение. «У нас есть кейсы с внедрением систем мониторинга на автозаводах «Москвич», «УАЗ», «СарыАркаАвтопром» и Belgee», - говорит Виктория Чирва.
Свое и чужое
«Если проблему можно предотвратить, это очень хорошо. И система мониторинга, в том числе работы оборудования, – это повышение физической эффективности производства как такового, - уверен главный редактор Quto.ru (входит в Rambler&Co) Максим Ракитин. - То есть не решать проблему, когда она уже случилась, а спрогнозировать и принять меры до того, как произошла поломка. И насколько я понимаю, сейчас «Соллерс» у нас один из лидеров, если не лидер в плане такого мониторинга».
«Существуют датчики, существует возможность полученные данные анализировать, а значит, спрогнозировать, что вот этот станок пора обслужить, чтобы избежать его аварийной остановки в течение ближайшей недели», - вторит Ракитину глава «Механики». По его словам, в университете имени Баумана еще много лет назад предложили «вариант по вибрациям». «Это косвенные признаки, очень важные для турбин и ряда других изделий, они позволяют диагностировать большое количество параметров, в т.ч. потенциального износа», - продолжает собеседник Mashnews.
«Мы используем различные комплексные решения для автоматизации производства, - уточняют в PROF-IT Group. - Сейчас это в основном отечественные разработки: наши собственные и наших технологических партнеров. Цифровая трансформация подразумевает создание ядра внутри компании, которое будет объединять разные уровни бизнес-процессов на сквозной основе, в том числе с привлечением ERP-систем плюс уровни MES и QMS».
Если говорить об онлайн-комплексах в целом, решения бывают не только покупные, как в случае с «Соллерсом»: например, производитель из Петербурга «БИГ Фильтр» пользуется собственной программой.
Н – нейросеть, Э – экономия
Важно, что речь идет не только о прогнозировании аварийных ситуаций, а об общем контроле над производственным процессом. Возможно, это шаг к всеобщей цифровизации, полагает Дмитрий Даньшов, - сделать в дальнейшем так, чтобы участки с участками, станки со станками могли «договариваться» без участия человека. Похоже, без помощи ИИ не обойтись.
«Системы мониторинга есть на китайских и японских автозаводах, - напоминает Максим Ракитин. – Эта практика очень широко применяется, она невероятно полезна с точки зрения возможных затрат на ремонт оборудования и с точки зрения оценки работы предприятия в целом. В современных комплексах по большей части используется искусственный интеллект – один человек такой массив информации просто не переварит, ведь речь не об одном станке, не об одной линии. Визуально все это количество элементов отследить визуально просто невозможно».
Малолюдные высокопроизводительные линии, в том числе автокомпонентные, существовали в Китае уже 10 лет назад, утверждает гендиректор «Механики». Но роботы – одно, мониторинг – другое. И если первые работают сейчас повсеместно, то вторые только проходят процесс внедрения на производства. Эксперты уверены: через некоторое время системы мониторинга будут работать практически на всех заводах.
В «Соллерс», похоже, с этим согласны: «У нас есть планы по дальнейшей цифровизации других площадок группы. Так, мы уже начали успешно внедрять WINNUM на производственных мощностях Заволжского моторного завода», - говорит Алина Комарова.
«Цифровизация производства становится приоритетом предприятий промтеха. При этом компании стали более амбициозно смотреть на весь спектр инновационных решений. Мы наблюдаем повышение уровня цифровой зрелости среди наших заказчиков, что не может не радовать. Автоматизация и цифровая трансформация дает как минимум стабильность и эффективность процессов, как максимум – возможность быть на шаг впереди и закладывать базу нового формата работы всего рынка», - заключает Виктория Чирва.
АвтоВАЗ тоже занимается обновлением. Так, сообщалось, что в этом году Тольяттинский госуниверситет должен поставить на Волжский автозавод отечественный измерительный комплекс для систем автоматического контроля геометрической точности размеров деталей двигателя. Это позволит провести на АвтоВАЗе глубокую модернизацию зарубежной линии автоматического контроля итальянской компании Marposs. Она действует уже больше 45 лет.