Атом, космос, авиастроение: Россия остается зависимой от ферросплавов из-за рубежа
Структура «Росатома» закупает ферросплавы почти на 14 млрд рублей. Скорее всего, они будут поставлены из-за границы. Эти материалы выпускаются в стране в недостаточном количестве либо не производятся вовсе. Отечественные предприятия специального машиностроения продолжают испытывать дефицит ферросплавов. Mashnews разбирался в проблемах и перспективах стратегического направления металлургии.
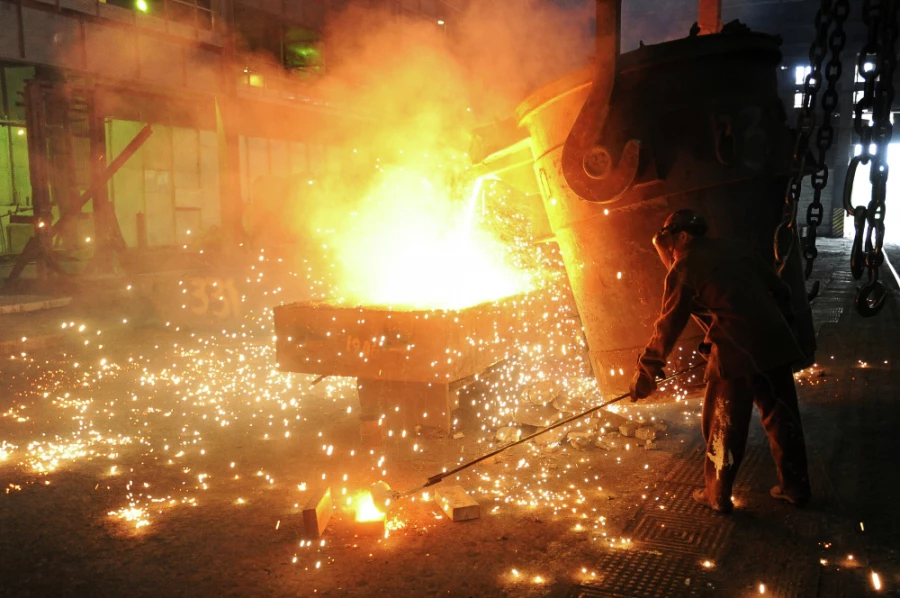
Миллиардный импорт
АО «АЭМ-Технологии» (машиностроительный дивизион «Росатома») провело закупку крупной партии малотоннажных ферросплавов. В списке есть ферромолибден, ферротитан, феррованадий, феррониобий и ферровольфрам. Итоги закупочной процедуры опубликованы 2 апреля. Название фирмы-поставщика не обнародовано.
Материалы общим объемом свыше 2,6 тыс. тонн должны быть поставлены до конца 2029 года. Цена контракта на день подведения итогов закупки превышает 13,9 млрд рублей, или 164,4 млн долларов США – именно в этой валюте заключен договор с поставщиком. Это свидетельствует о том, что основная часть ферросплавов будет поступать с мирового рынка.
Объективные причины для импорта – отсутствие достаточного внутреннего предложения, например, по самому востребованному из закупаемых материалов – ферромолибдену, который составляет половину объема всей закупки – 1,38 тыс. тонн.
Ферросплавы высокой чистоты необходимы для производства спецсталей для ракетно-космической индустрии, авиастроения и атомной энергетики. Так, металлурги завода «АЭМ-Спецсталь» только что начали ковку заготовок для последующего производства элементов корпуса реактора шестого энергоблока венгерской АЭС «Пакш-2», об этом «Росатом» сообщил 7 апреля.
Самообеспеченность страны малотоннажными ферросплавами является задачей уровня национальной безопасности.
СПРАВКА MASHNEWS
- АО «АЭМ-Технологии» расположено в Колпино (Санкт-Петербург), входит в «Росатом», производит оборудование для атомной энергетики, предприятий нефтегазохимического комплекса, теплоэнергетики и других отраслей. В структуру предприятия входят инжиниринговый центр и четыре производственных комплекса. Последний раз финансовые показатели публиковались за 2021 год. Тогда выручка составила 32,8 млрд рублей, чистая прибыль - 5,1 млрд рублей.
Мощностей хватает, но нет сырья
Совокупная мощность ферросплавных предприятий России избыточна для удовлетворения внутреннего спроса. Основная часть крупнотоннажных ферросплавов (феррохром, ферротитан, ферромарганец, ферросиликомарганец) поступает на экспорт, но производятся эти материалы по большей части из импортного сырья.
С хромом и титаном ситуацию удалось переломить. Наибольшая зависимость сейчас по марганцу: отечественные марганцевые руды относятся к бедным, труднообогатимым, в них в значимом количестве содержатся вредные примеси. Покупать сырье за рубежом выгоднее, даже с учетом действующих санкций. Есть проблемы и с выпуском на собственном материале малотоннажных ферросплавов.
«Что мы практически не выпускаем, так это феррониобий. Его применяют для производства жаропрочных сталей в авиации, нержавеющих низколегированных сталей в машиностроении, судостроении, трубной промышленности. Плюс пентаоксид ниобия высокого качества используется в производстве металлического ниобия и ниобиевых лигатур для спецсплавов. Получаемый из него феррониобий сильно дорогой. В итоге Россия ежегодно импортирует тысячи тонн этого материала из Бразилии и Канады», - рассказывает директор Научного центра комплексной переработки сырья ЦНИИчермет, кандидат химических наук Антон Волков.
Единственный отечественный источник сырья – пентаоксид ниобия Соликамского магниевого завод. Его получают из лопаритового концентрата Ловозерского горно-обогатительного комбината, сейчас он выпускается в недостаточном для страны количестве. Но горнорудный дивизион «Росатома» работает над расширением добычи породы и отдачи месторождений.
«В Левозерский ГОК в прошлом году инвестировали порядка 400 млн рублей – больше, чем вложили бывшие собственники за десять лет. В 2025 году введены в эксплуатацию три новых очистных блока, идет обновление парка спецтехники. В общей сложности подготовлены к добыче запасы до 63 тыс. тонн руды. Это гарантирует предприятию необходимый объем добычи сырья, а от нее в прямой зависимости находится объем выпуска пентаоксида ниобия», - сообщил Mashnews официальный представитель Соликамского магниевого завода.
Добычу молибдена в России осуществляет только одно предприятие – Сорский ГОК. Ввиду сложного состава руд освоение месторождений напрямую зависит от уровня мировых цен на молибден. Они в последние годы настолько низки, что из-за отсутствия экономической целесообразности были законсервированы не только проекты освоения новых участков недр, но и действующий ранее Жирекенский ГОК.
Промышленный рассинхрон
В то же время российские производители ферромолибдена, не имеющие собственной сырьевой базы, испытывают дефицит сырья и вынуждены ежегодно импортировать около 3 тыс. тонн молибденового концентрата, что составляет около 50% объёма его потребления.
В 2024 году в России, по данным ТК Solutions, было выпущено 2474 тонны ферромолибдена, что на 15,4% меньше объемов 2023 года. Небольшой рост отмечается на начало 2025 года, но производится этого продукта по-прежнему крайне мало, его импорт неизбежен при возрастающем спросе.
В вольфрамовой отрасли наблюдается отсутствие эффективной кооперации переработчиков сырья и производителей товарных продуктов. В результате объем экспортируемого вольфрамового концентрата почти в 1,5 раза превышает объём импортируемого. Это обусловлено географическим положением добытчиков сырья и его переработчиков.
По ванадию Россия является одним из мировых лидеров, но есть проблемы с отдельными видами продукции. Страна производит много пентаоксида ванадия, ванадиевого шлака и феррованадия, но оксиды ванадия с более низким содержанием примесей поступают из-за рубежа. Их используют для получения специальных лигатур, применяемых, например, в авиакосмической отрасли.
Технологические разрывы
Помимо трудностей с добычей сырья и выпуском отдельных видов металлов и сплавов, серьезной проблемой является деградация машиностроительной отрасли. Ферросплавы производят в электропечах. В советское время была создана мощная научно-производственная база, включающая институт ВНИИЭТО с опытным заводом и предприятие «Сибэлектротерм» с конструкторским бюро и собственным заводом.
«Сейчас от двух отраслевых гигантов остались осколки в виде нескольких небольших фирм, занимающихся изготовлением документации по наработкам прошлых лет. В итоге сроки изготовления печного оборудования выросли, по некоторым проектам число субподрядчиков доходит до 40. Одни делают электротехническое оборудование, другие гидравлическое, третьи – ванну печи. Сам завод «Сибэлектротерм» признан банкротом и выставлен на торги», - рассказал Антон Волков.
Для производства ферросплавов нужны вспомогательные материалы и оборудование. Тут есть вопросы с огнеупорным производством. Недостаточный объем выпуска высококачественного магнезитового сырья, увеличение стоимости добычи на Саткинском месторождении компенсируются за счет импортных поставок – около 60 тыс. тонн в год.
Графитированные электроды для печей большой мощности (сталеплавильные и ферросплавные) в России делают из импортного игольчатого кокса. Потребность в самих электродах также почти наполовину покрывается за счет импорта.
Если говорить о металлургии в целом в плане углеродных материалов, то острейшими проблемами импортозамещения являются производство специального пекового кокса, создание углеродных волокон, получение связующего для огнеупорных масс доменного производства. Все эти вопросы в контексте достижения технологического суверенитета только предстоит решить.
Эксперты отмечают, что по отдельным предприятиям ферросплавной отрасли есть развитие и локальные успехи. Так, «ЕВРАЗ» строит в Туле вторую очередь производства пентаоксида ванадия и феррованадия. На Серовском заводе ферросплавов освоили технологию выплавки особо чистого ферросилиция и выплавку ферросплавов с низким содержанием фосфора и кремния. Производство марганцевых ферросплавов наладили Западно-Сибирский электрометаллургический завод, Челябинский электрометаллургический комбинат, Саткинский чугуноплавильный завод, Косогорский металлургический завод.
Государство – главный игрок
Совсем недавно к нам по импорту поступало не сырье, а готовые марганцевые ферросплавы. То есть сейчас отечественные предприятия начали создавать добавленную стоимость, но отраслевого баланса по номенклатуре выпускаемой ферросплавной продукции явно не хватает, а ее применение в промышленности достаточно вариативно.
Прежде всего требуется рост внутреннего спроса, его может обеспечить развитие производства качественной стали, в том числе нержавейки и других спецсталей с повышенными прочностными и антикоррозионными свойствами. Первый такой проект готовится к запуску в Волгоградской области поддерживается на высшем уровне.
Крупным потребителем выступает отрасль специального машиностроения, где есть перспективы мирового технологического лидерства – в первую очередь, это атомная энергетика, авиакосмическая сфера и военно-промышленный комплекс.
Государство уже предприняло действия по установлению контроля над ферросплавным сектором металлургии. В 2024 году были национализированы крупнейшие предприятия: Челябинский электрометаллургический комбинат, «Кузнецкие ферросплавы» и Серовский завод ферросплавов. Уже год эти активы находятся под управлением Росимущества, что свидетельствует о неопределенности с распределением богатого наследства. Первым в очереди ранее назывался «Ростех», но официальных решений на этот счет по-прежнему нет.
Тем временем из актуальной повестки привлекает к себе внимание активность «Росатома». Связанные с ним структуры приобрели часть имущества АО «Гидрометаллург» в Кабардино-Балкарии. Ожидается, что покупатель организует новый бизнес, возможно, даже построит новое предприятие. А завод, ранее выпускавший оксиды вольфрама и молибдена и проходящий процедуру банкротства, планирует на оставшихся после распродажи мощностях возобновить производство вольфрамового продукта из давальческого сырья.
Очевидно, что оживление в отрасли есть, осознание необходимости самообеспечения редкими и ценными материалами, без которых не может обойтись современная промышленности, переросло в стратегические инициативы. Потребуются серьезные вложения для технического перевооружения и меры господдержки – административной и финансовой. В приоритетных отраслях и ключевых проектах цена достижения цели не будет иметь значения, особенно если при оплате речь только о деньгах. У крупнейшего инвестора и главного бенефициара они найдутся.